STL - Stop Turn Locking System
- Standard Range
- Stopping:
- Up to 285 000 Nm
- Turning:
- 227 000 Nm
- Locking:
- 600 000 Nm
The STL Systems are "multi-function" units, all contained within one interface. It is indeed a modular system that you can choose the function(s) needed. All from single, S (Stopping) T (Turning) or L (Locking) functions. Combined dual or triple functions in terms of SL, ST, TL, to a complete STL system can be selected. Each system contain a unique control system that communicate and integrate with superior system for easy operation and control.
- Individual stopping, turning and locking functions
- Dual functions: Stop and Turn, Stop and Lock, Turn and lock
- A complete, turning and locking system
- Control systems designed and/or customized to meet platform unique integration
- Hydraulic
- Electric
- Manual
- Standard or Custom packages
- Shock and vibration approved configurations
- Hand held control units
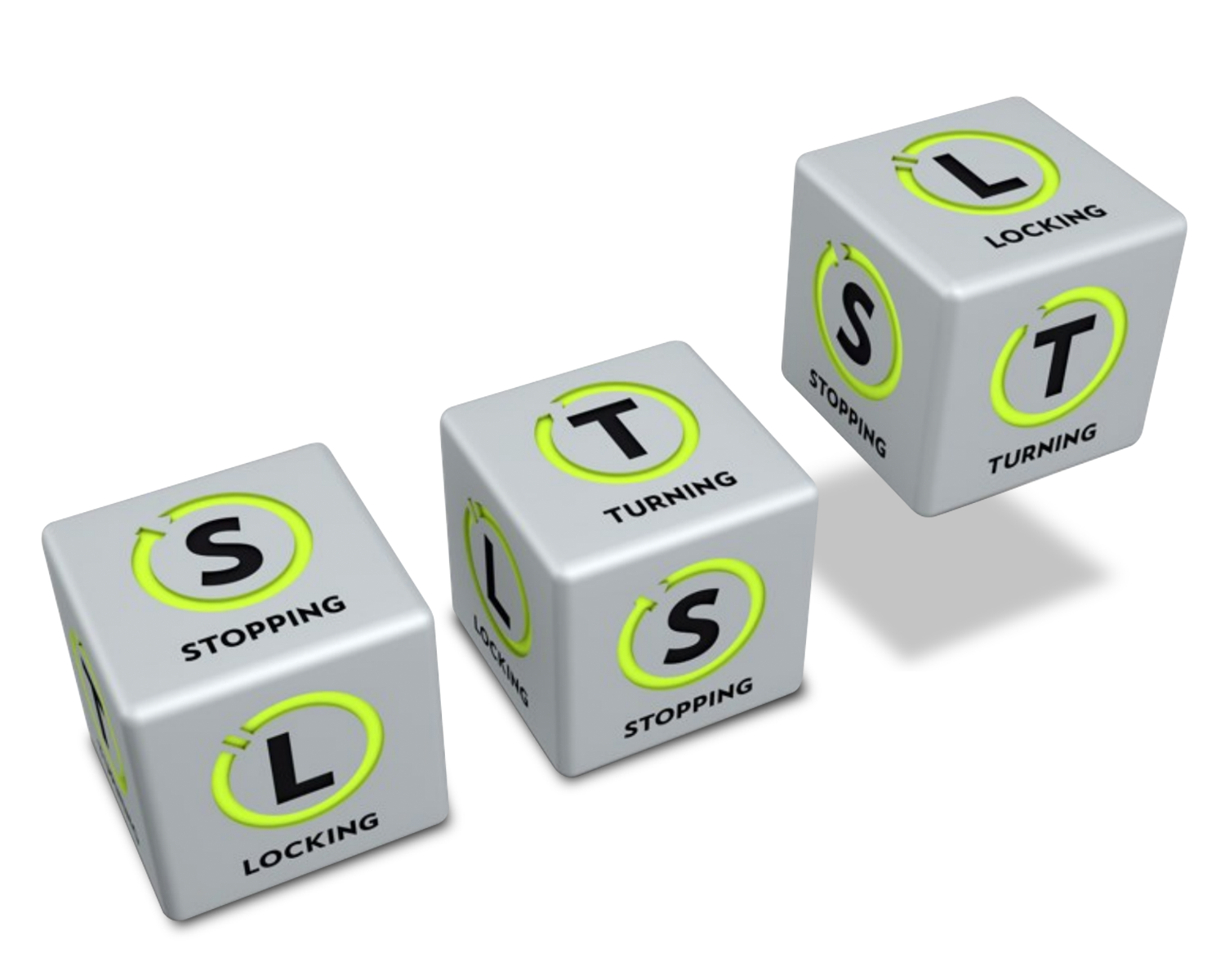
Whether at sea or based on land, STL Systems give you complete control over your stopping, turning and locking functions.
Stopping, Turning and Locking (STL) systems are precision engineered and fully modular, making it possible to choose from the functions to create a system which fits your application:
- Individual Stopping, Turning or Locking functions
- Dual Functions:
- Stopping & Turning
- Stopping & Locking
- Turning & Locking
- Complete STL-System with all functions
- Fully automatic control
- Semi-automatic control
- Fully manual control
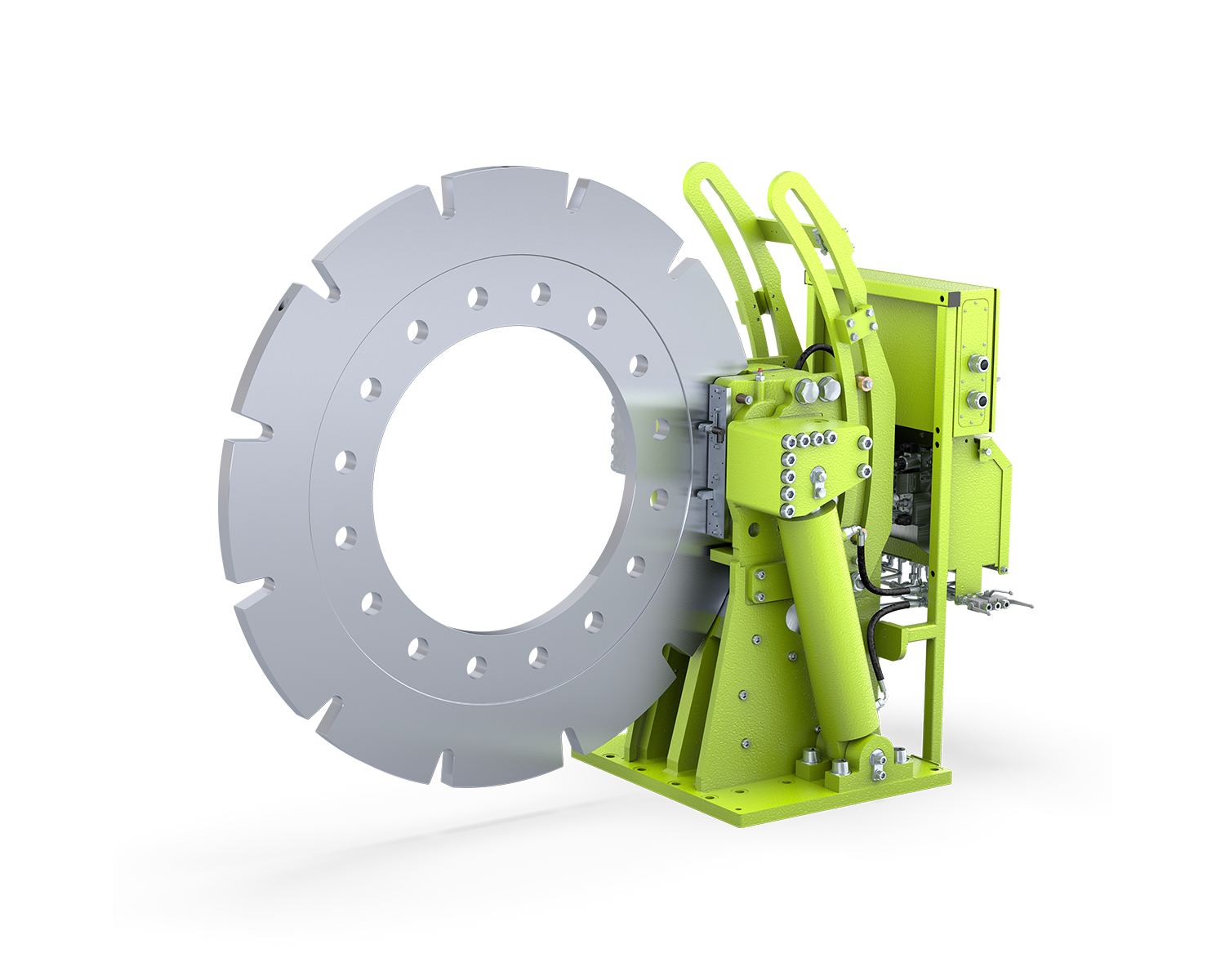
Stopping, index Turning and Locking (SiTL)
Advantages:
- Easy engagement and disengagement even with residual forces present
- Turning function is index turning with hydraulic cylinders
- Controlling can be done fully remotely, locally with push button interface, or as combination of the two controls
- Low maintenance overtime with increased personnel safety
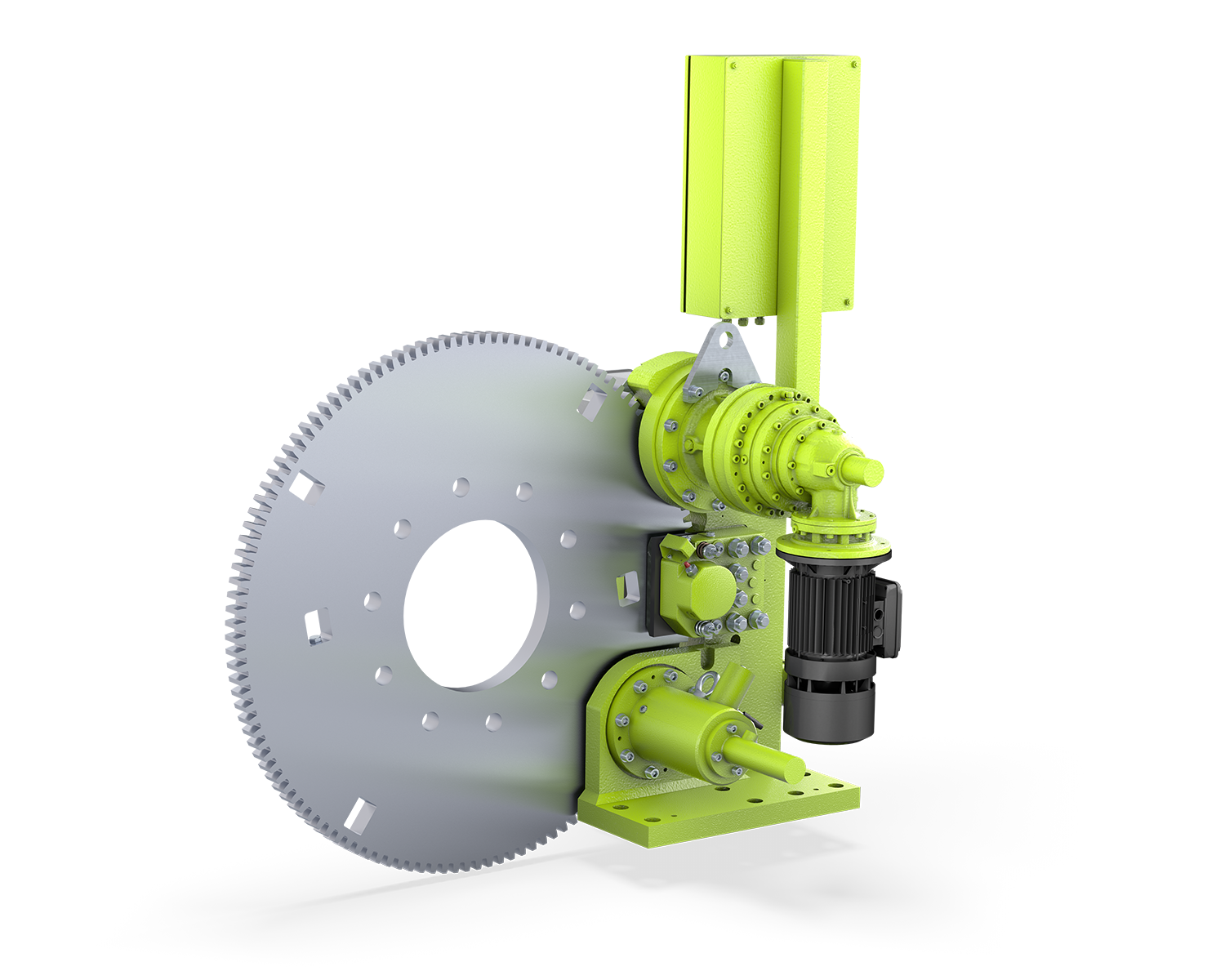
Stopping, continuous Turning and Locking (ScTL)
The electric powered continuous STL could be a preferred selection in low-range to midrange torque applications when a continuous turning operation is required and/or when manual operating has limited possibilities.
Advantages:
- Easy engagement and disengagement even with residual forces present
- Turning function is continuous turning with electric motor and gearbox
- Controlling can be done fully remotely, locally with push button interface, or as combination of the two controls
- Low maintenance overtime with increased personnel safety
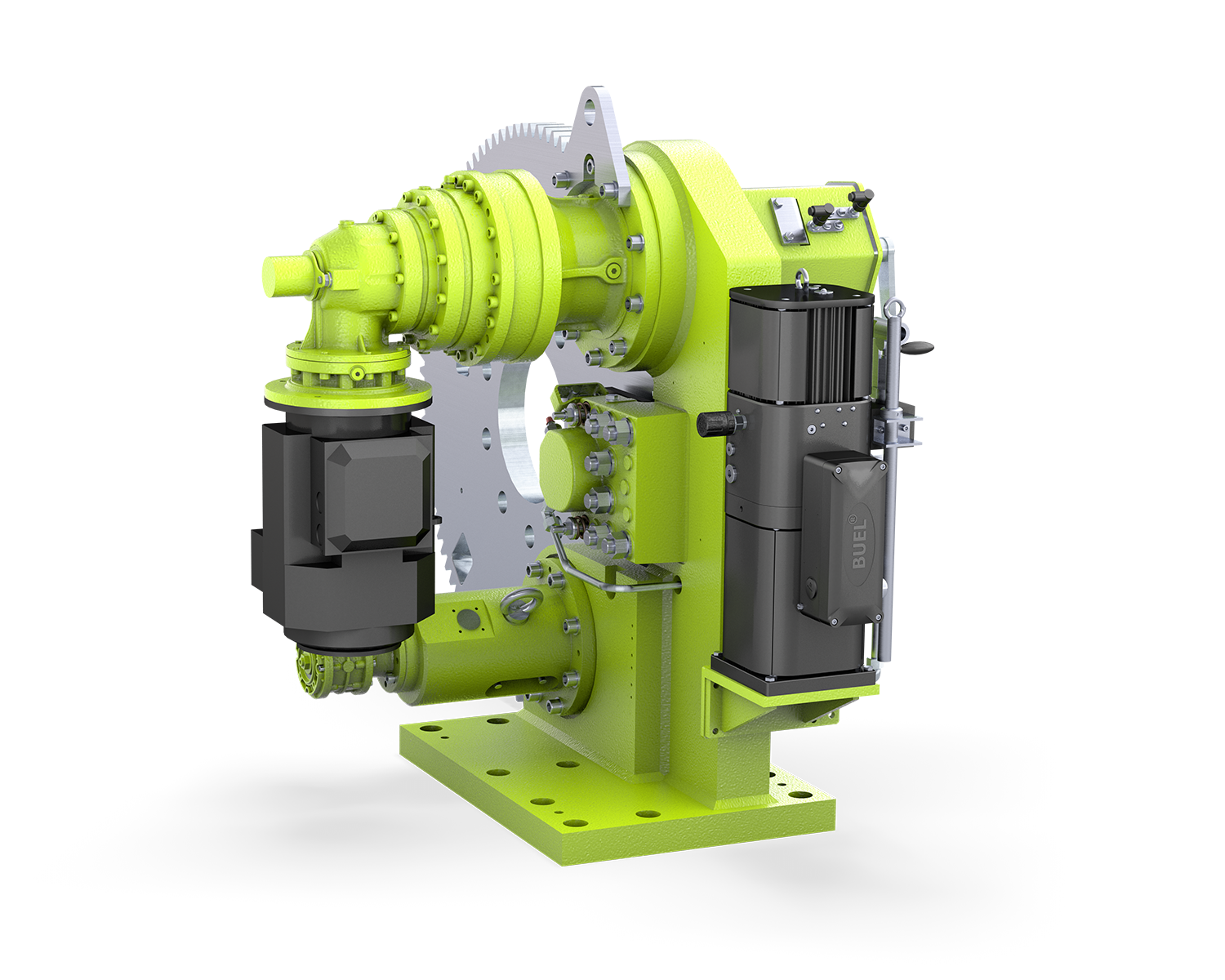
Stopping, continuous Turning and Locking (ScTL) with BUEL®
DELLNER BUBENZER’s compact, self contained BUEL® STL systems combine elements from STL with DELLNER BUBENZER’s patented BUEL® electrohydraulic thruster/power package.
Needing no external piping, the systems are compact, easy to install, and with the BUEL® using only half a litre of high performance synthetic oil (compared to up to 30 litres of hydraulic oil in standard hydraulic power units), are cheaper to run and enviromentally-friendly too.
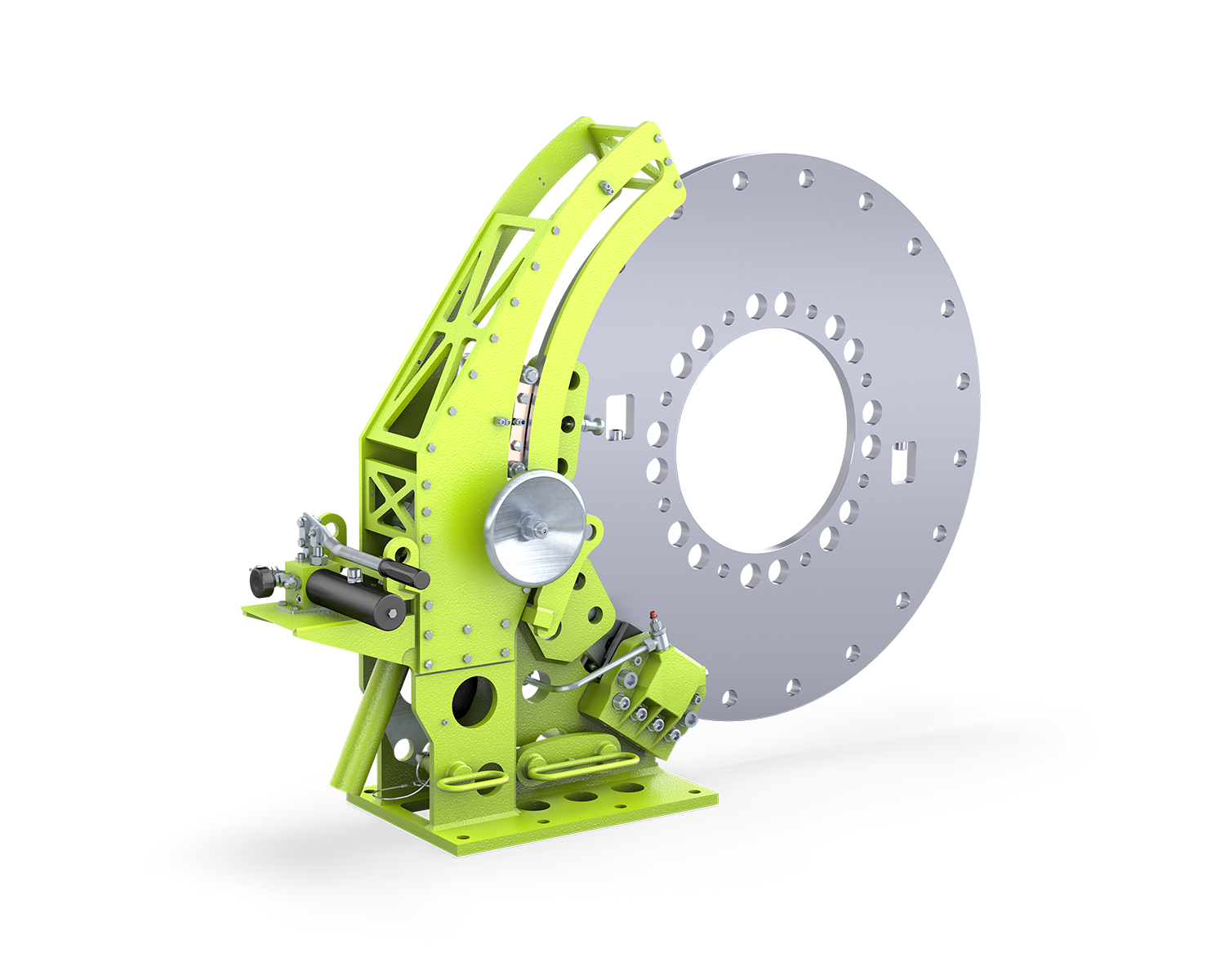
Fully Manual Stopping, index Turning and Locking (SiTL)
The electric powered continuous STL could be a preferred selection in low-range to midrange torque applications when a continuous turning operation is required and/or when manual operating has limited possibilities.
Advantages:
- Easy engagement and disengagement even with residual forces present
- Turning function is indexed turning with fully manual control
- Controlling is done fully locally, with provision for instruments for status detection (interlock)
- Fully independent from external power sources
- Low maintenance overtime with increased personnel safety
Additional PRODUCTS
- All
- Caliper / Disc Brakes
- Components & Accessories
- Couplings
- Drum & Band Brakes
- Hydraulic Systems
- Locking Devices
- Monitoring & Control Systems
- Motor Mounted Brakes
- Pneumatic Drum Clutches & Brakes
- Stop Turn Lock Systems
- Storm Brakes (Rail & Wheel Brakes)
- Thruster / BUEL®
- Wind Turbine Components
- WPT Disc Clutches & Brakes
These rail clamps are storm brakes suitable for high forces. They are self-blocking type; in case a force acts on the crane and tends to put the same into motion, they press on the rail sideways.
These rail clamps are storm brakes suitable for high forces. They are self-blocking type; in case a force acts on the crane and tends to put the same into motion, they press on the rail sideways.
The DH hydraulic power packs deliver pressure up to 200 bar and can be delivered with optional hydraulic cabinets and electrical terminal boxes.
The EBA is a powerful drum brake with braking torques from 24 (ft-lb) to 9000 (ft-lb) that meets AISE (TR11) & NEMA (ICS 8) standards.
The EBH series is designed according to DIN 15435. This design is very compact and can be used in tight motor gearbox combinations.
The EBN series is designed according to DIN 15435 and has been in use in various industries for decades. EBN-2St modification: the drum brakes solution for Bridges and Sluice Systems
The FKE is best suited for applications with light starting and stopping loads. It is also commonly used as a slip clutch or tension brake within light horsepower and torque applications.
The FKR is often referred to as a coupling, as its expanding neoprene rubber facing engages the interior diameter of the drum directly. The resulting friction generates significant torque within a small package.
The FK is well suited as a clutch or brake for a variety of high speed and low to medium torque power transmission applications where high heat generation is not a factor.
The FKT is well suited for applications with the most demanding equipment where severe clutching and braking is required.
The FM is designed and manufactured for marine applications, mainly for use on diesel-driven reduction gears.
Our hand pump can be used to simply activate the Dellner brake calipers. It also acts as a back up system for the primary pressure supply system.
The hydraulic rotary actuator is a device which transform hydraulic power (pressure and flow) in mechanical power: torque and angular speed.
A hydraulic rotor lock offering up to 250 bar pressure with an activation time of 60 seconds.
We offer three models of the JHS-RLH-240 hydraulic rotor lock – the GL Type Certified JHS-RLH-240, the JHS-RLM-240 and the JHS-RLH-240-154. All these locks deliver up to 250 bar pressure with an activation time of just 35 seconds.
Manually activated rotor lock used for safety purposes during maintenance operations to stop the rotor mechanically. The maximum lateral force is 6400 N and the standard stroke is 95 mm. Other strokes are available upon request.
These couplings are for use in application with high dynamic loads. Damping of peak torques and vibrations as well as electrical insulation between motor and gearbox are further reasons for the use of this coupling type.
The KBSD Gear Couplings are for use in machinery where a torsionally rigid torque is required, especially on frequently varying loads and speeds.